立式硫化罐的工作原理是基于橡胶硫化的化学反应需求,通过提供特定的温度、压力和时间条件,使橡胶分子链发生交联反应,具体如下:
1. 加热原理:立式硫化罐通常采用蒸汽加热或电加热方式。蒸汽加热时,蒸汽通过管道进入硫化罐内,与罐内的橡胶制品进行热交换,使橡胶制品升温。电加热则是利用电加热元件产生热量,加热罐内的热介质(如空气等),进而使橡胶制品受热。热量传递到橡胶制品上,使橡胶分子获得足够的能量开始运动,为后续的硫化反应创造条件。
2. 加压原理:随着加热过程的进行,罐内的气体(如蒸汽或空气)受热膨胀,导致罐内压力升高。此外,也可通过向罐内充入压缩空气或其他气体来增加压力。适当的压力能使橡胶制品在硫化过程中更好地保持形状,防止出现变形等问题,同时促使橡胶与硫化剂充分接触和反应,使硫化反应更均匀、更充分地进行。
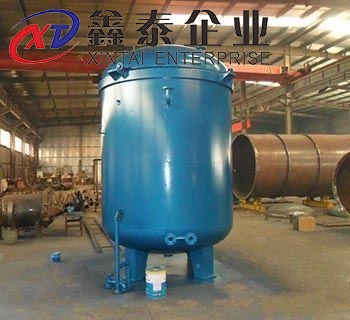
3. 硫化反应原理:当橡胶制品被加热到合适的硫化温度并处于一定压力下时,橡胶中的双键与硫化剂(如硫、硫化物等)发生化学反应,形成交联结构。这种交联结构使橡胶分子从线性或支链型结构转变为三维网状结构,从而提高橡胶的强度、弹性、耐磨性、耐热性和耐老化性等物理机械性能。
4. 冷却原理:硫化完成后,需要对橡胶制品进行冷却。通常是停止加热,并通过冷却介质(如水或空气)对硫化罐进行降温,使橡胶制品温度降低到可以取出的温度范围。冷却过程可以使橡胶的交联结构进一步稳定,防止在后续处理或使用过程中出现性能变化。
立式硫化罐对产品质量的影响主要体现在以下方面:
1. 温度控制对产品质量的影响
温度均匀性:若硫化罐内温度不均匀,会导致橡胶制品不同部位的硫化程度不同。温度高的区域可能硫化过度,使橡胶变硬变脆,降低产品的柔韧性和抗疲劳性能;温度低的区域则可能硫化不足,橡胶的强度、弹性等性能达不到要求,产品容易出现变形、撕裂等问题。
温度稳定性:温度波动过大,会使橡胶的硫化反应进程不稳定,影响交联结构的形成。可能导致产品性能波动大,批次之间的质量一致性差,降低产品的整体质量水平和市场竞争力。
2. 压力控制对产品质量的影响
压力大小:压力不足,橡胶制品在硫化过程中可能无法充分压实,内部可能存在气泡、空隙等缺陷,降低产品的致密性和强度。压力过大,则可能使橡胶制品产生过度变形,甚至损坏模具或设备,同时也可能导致橡胶分子链过度交联,使产品变硬变脆,影响其使用性能。
压力均匀性:罐内压力分布不均匀,会使橡胶制品各部位受到的压力不同,导致产品厚度不均匀,或在压力大的部位出现局部过硫现象,影响产品的外观和性能。
3. 硫化时间对产品质量的影响
时间过短:橡胶分子链的交联反应不充分,产品的物理机械性能无法达到最佳状态,如强度、弹性、耐磨性等较差,产品使用寿命短。
时间过长:会使橡胶发生过硫现象,橡胶分子链过度交联,产品变硬变脆,失去良好的柔韧性和弹性,同时也会增加生产成本,降低生产效率。
4. 冷却过程对产品质量的影响
冷却速度:冷却速度过快,橡胶制品内部可能产生较大的内应力,导致产品在后续使用过程中出现开裂、变形等问题。冷却速度过慢,则会延长生产周期,降低生产效率。
冷却均匀性:冷却不均匀会使橡胶制品各部位收缩不一致,产生内应力,影响产品的尺寸稳定性和外观质量,严重时会导致产品报废。