立式硫化罐自动化控制系统对于实现精准温控与压力管理至关重要,以下是其详细介绍:
系统构成
传感器模块
温度传感器:通常采用热电偶或热电阻传感器,安装在硫化罐内部不同位置,用于实时测量罐内温度。这些传感器能精确感知温度变化,将温度信号转换为电信号,为控制系统提供准确的温度数据。
压力传感器:一般选用高精度的压力变送器,安装在硫化罐的罐体上,用于监测罐内压力。它可以将压力信号转化为标准的电信号,以便控制系统进行处理和分析。
控制模块
可编程逻辑控制器(PLC):作为控制系统的核心,PLC接收来自传感器的信号,根据预设的硫化工艺参数进行逻辑运算和处理,然后输出控制信号,对加热、加压等设备进行精确控制。它具有可靠性高、抗干扰能力强、编程灵活等优点,能够适应复杂的工业环境。
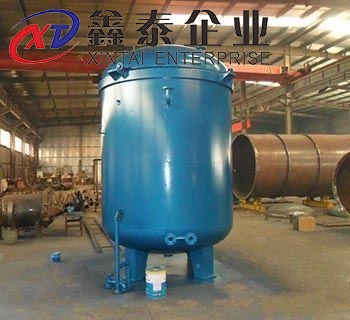
工业计算机(IPC):主要用于实现人机交互功能,操作人员可以通过IPC的显示屏直观地查看硫化罐的温度、压力等实时数据,设置和修改硫化工艺参数,还能对历史数据进行存储、查询和分析,为生产管理提供依据。
执行模块
加热执行机构:如果是蒸汽加热,通常由电动调节阀控制蒸汽的流量,根据PLC的控制信号,调节阀自动调节开度,从而精确控制进入硫化罐的蒸汽量,实现温度的精确控制。若是电加热方式,则通过可控硅调功器等设备来调节电加热元件的功率,达到控制温度的目的。
加压执行机构:一般由空气压缩机和气动调节阀组成,空气压缩机为硫化罐提供压缩空气,气动调节阀根据PLC的指令调节压缩空气的进气量,从而精确控制罐内压力。对于需要充入其他气体进行加压的情况,也有相应的气体供应和调节装置。
精准温控与压力管理实现方式
精准温控
PID控制算法:控制系统采用PID(比例积分微分)控制算法,根据温度设定值与实际测量值的偏差,自动调整加热执行机构的输出,使温度偏差逐渐减小。比例环节能快速响应温度偏差,积分环节用于消除稳态误差,微分环节则可预测温度变化趋势,提前进行调节,从而实现温度的精确控制。
分段式温度控制:根据橡胶硫化工艺的不同阶段,设定不同的温度值,控制系统按照预设的温度曲线进行分段式控制。例如,在升温阶段快速将温度升高到硫化温度,在保温阶段保持温度稳定,在冷却阶段又能按照设定的速率降低温度,确保橡胶制品在各个阶段都能获得合适的温度环境。
温度均匀性补偿:通过在硫化罐内设置多个温度传感器,实时监测各点温度,当发现温度不均匀时,控制系统会根据各点温度偏差,对相应区域的加热量进行微调,以保证罐内温度的均匀性,从而提高产品质量的一致性。
压力管理
压力定值控制:操作人员在控制系统中设定好硫化过程所需的压力值,压力传感器实时监测罐内压力并反馈给PLC,当实际压力低于设定值时,PLC控制加压执行机构增加进气量,使压力上升;当压力高于设定值时,则控制执行机构减少进气量或进行排气,使压力保持在设定值附近,确保压力稳定。
压力与温度的协同控制:在橡胶硫化过程中,压力与温度相互关联。控制系统会根据温度的变化自动调整压力设定值,以保证硫化反应在合适的压力和温度条件下进行。例如,在升温阶段,随着温度的升高,适当增加压力,使橡胶制品在良好的状态下进行硫化反应。
压力安全保护:设置了多重压力安全保护机制,当罐内压力超过安全上限时,系统会自动启动泄压装置,防止压力过高引发安全事故。同时,还会发出声光报警信号,提醒操作人员及时处理。
优势
提高产品质量:通过精准的温控和压力管理,确保橡胶制品在硫化过程中温度和压力均匀、稳定,使橡胶分子交联反应充分且一致,从而提高产品的物理机械性能和尺寸稳定性,降低次品率。
提升生产效率:自动化控制系统能够快速、准确地按照预设的工艺参数进行控制,减少了人工操作的时间和误差,缩短了硫化周期,提高了生产效率。
降低劳动强度:操作人员只需在人机界面上进行参数设置和监控,无需频繁地手动调节加热、加压设备,大大降低了劳动强度,改善了工作环境。
实现生产数据追溯与管理:系统能够实时记录和存储硫化过程中的温度、压力等数据,方便管理人员对生产过程进行追溯和分析,为工艺优化和质量改进提供依据,有助于实现生产的精细化管理。